Socks manufacturing is not a high-tech industry, but it involves many detailed processes. Each section of the production must coordinate with each other to ensure quality requirements and time-controlling. In this post we will talk about socks manufacturing process in detail.
The whole socks manufacturing process does involve many steps, and the coordination between these steps makes the whole process time-consuming. Sorting out all steps above, there are overall 7 steps that we will mainly talk about as follows:
- Pattern coding
- Yarn preparation
- Knitting socks
- Linking/Sewing socks
- Boarding
- Pairing&Labelling socks
1. Pattern coding
What our clients provide us are the sock designs, however sock knitting machine are not that intelligent to read the designs directly. A professional coding team who are familiar with sock pattern and mahine mechanism will do this job. They will transfer your vector designs into bitmap designs and then codes that the knitting machines can read. Every pixel of the bitmap design means a thread with the specific color will be knitted through.
Different needles of knitting machine means the widths of flat bitmap designs are different, 96N, 144N, 168N, 200N of machines means the widths are 96, 144, 168, 200 pixels, respectively. And the limit of threads count is the reason why socks can’t present gradient or detailed patterns.
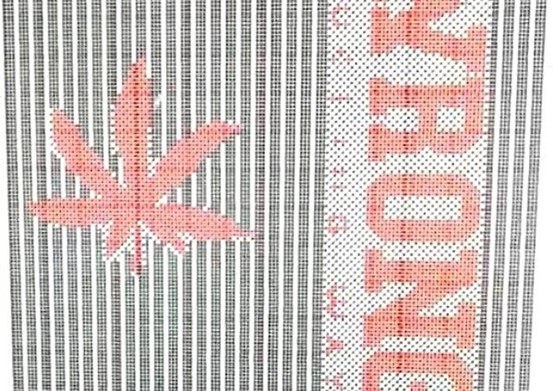
2. Yarn Preparation
In the order details we have confirmed 2 important things regardign yarn: Composition and Colors.
On how to choose a proper composition for your socks.
For normal and combed cotton, we have over 1000 colors in stock that are able to match your pantone colors.
For other yarn like merceized cotton, wool, etc, we will make custom dyed yarn according to your specified pantone tcx colors.
3. Knitting socks
Using programmed codes in step 1, multitude of needles then knit the various threads into a series of interlocking loops. Computerized sock knitting machines work at high speeds and can easily be programmed to produce a wide variety of socks. 1st inline-inspection is implemented here to avoid mistakes like length, trimming, interlocking etc.
4. Linking/Sewing socks
Knitting makes a cylinder tube, thus we need to the sewing process in order to link the seperated toe parts together. This is usually done by machine, which is quick. Sometimes this process is also done by manual work, which costs a lot of time. Since the socks are sewed one by one, our skilled workers can easily find defective socks and clear them away from the majority, which is the 2nd inline-inspection.
5. Boarding socks
The boarding process is actually implemented to keep the socks in good shape, so that they can easily be paired and packed. One more thing to note here is that the boarding step also keep the socks clean and soft by experiencing steams under a fixed pressure and temperature. After boarding, the socks will naturally dryed.
6. Pairing&Labelling socks
This is the final inspection step to see if there is any deflection on the socks. The left and right socks are paired together and then passed on to be private labelled. You can choose hangtags or bands to label your socks.